Automation has transformed work from manual farm tools to complex factories and now intelligent machines powered by AI. You can see this evolution in the shift from simple mechanical devices to large-scale assembly lines, and eventually to robots and computer-controlled systems. Each step has increased efficiency and changed job roles, making work more specialized and automated. If you want to understand how this journey continues today, you’ll find plenty more to uncover as history evolves.
Key Takeaways
- Automation evolved from manual craftwork to mechanized factory systems, significantly increasing productivity and standardization.
- The development of control systems, from relay logic to digital PLCs, enabled flexible, computer-based manufacturing automation.
- Assembly lines and robotics revolutionized mass production, enhancing efficiency, safety, and product quality across industries.
- AI and advanced automation are transforming workplaces, creating new roles while displacing traditional jobs, emphasizing adaptability and resilience.
- Throughout history, automation has continuously redefined work, shifting skills requirements and societal structures from farms to factories to AI-driven industries.
The Dawn of Mechanical Innovation and Industrial Shift
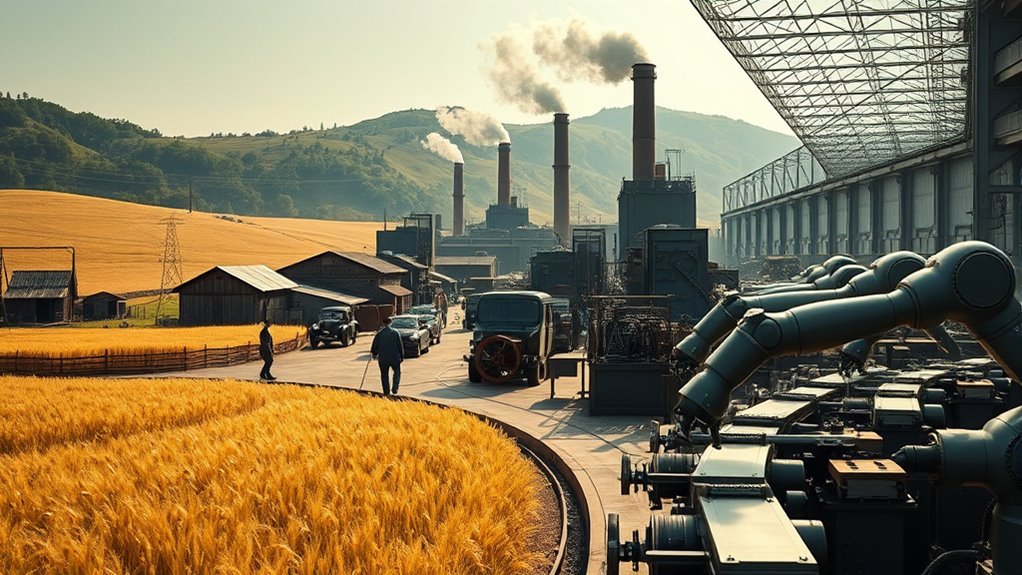
The dawn of mechanical innovation marked a turning point in industry, transforming how goods were produced and laid the groundwork for modern manufacturing. You see, in 1764, James Hargreaves invented the spinning jenny, letting one worker spin multiple spools at once and dramatically boosting yarn output. Then, in 1775, Richard Arkwright developed powered textile mills driven by steam engines, creating the first integrated factory system. Samuel Crompton’s spinning mule in 1779 combined earlier machines to produce finer, stronger thread on a large scale. By 1785, Edmund Cartwright patented the power loom, mechanizing weaving and increasing fabric production speed. These innovations marked the shift from home-based crafts to centralized factories, setting the stage for rapid industrial growth and mechanized mass production. The introduction of steam power in textile mills further accelerated this transformation, enabling factories to operate more efficiently and on a larger scale. This era also saw the rise of mechanized assembly lines, which would revolutionize manufacturing processes in the following centuries. Additionally, the development of heat pump technology has modernized heating and cooling, enhancing factory efficiency and worker comfort. Moreover, the integration of AI-driven automation is now poised to redefine manufacturing in the 21st century. Modern air purification systems are increasingly incorporated into factories to improve indoor air quality and protect worker health, reflecting ongoing technological advancements.
Electrification and the Rise of Automated Control Systems
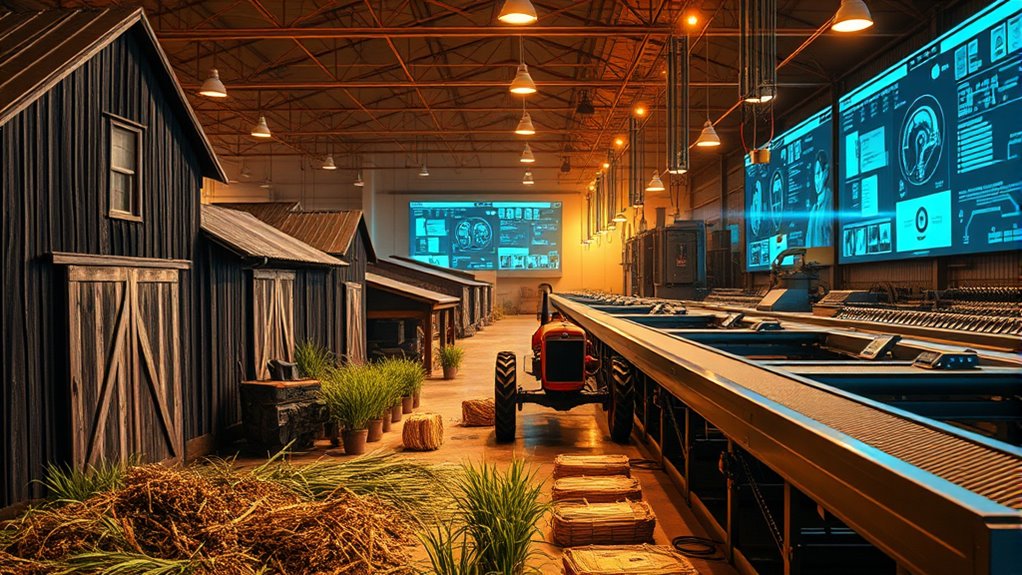
As factories shifted from steam engines to electric motors in the 1920s, they experienced a dramatic boost in efficiency and reliability. You’d notice higher output—around 30% more—thanks to electric motors’ efficiency and lower maintenance. This shift was supported by central electric power stations and substations, fueling increased demand for control instruments. Relay logic, introduced with electrification, revolutionized automation early on. By the late 1950s, solid-state digital logic modules replaced electro-mechanical relays, paving the way for programmable logic controllers (PLCs). Invented in the 1970s, PLCs transformed automation by replacing hard wiring with programmable systems, improving precision and efficiency. This technological advancement in control technology drove economic growth and reshaped manufacturing’s efficiency, setting the stage for further technological advances.
The Birth of Mass Production and Assembly Line Dynamics
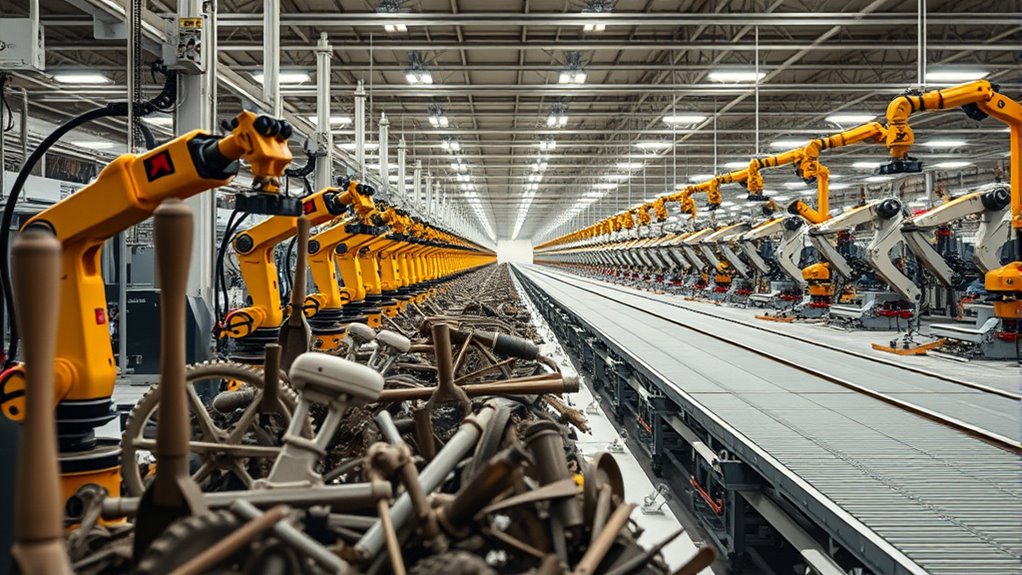
You can see how assembly line efficiency transformed manufacturing by dramatically reducing production time and costs. Standardization became essential, ensuring consistent quality across every product. This shift laid the foundation for modern mass production and automation. The introduction of the moving assembly line at Highland Park in 1913 exemplifies this revolutionary change, making it possible to produce vehicles on a much larger scale. Additionally, the adoption of industrial automation has further streamlined processes, paving the way for highly efficient manufacturing systems.
Assembly Line Efficiency
The development of assembly line efficiency revolutionized manufacturing by drastically reducing production times and increasing output. You can imagine how Ford’s 1913 Highland Park line cut car assembly from 12.5 hours to just 93 minutes, boosting productivity by over 1,300%. This shift enabled industries like meat-packing and appliances to scale up rapidly. By the late 1930s, assembly lines expanded globally, with Japanese automakers adopting these techniques. Key components included:
- Continuous flow of products through specialized workstations
- Even task distribution for ideal performance
- Workstation specialization to maximize efficiency
These innovations allowed factories to produce more with fewer resources, lowering costs and increasing revenue. As efficiency improved, so did labor productivity and output, transforming manufacturing into a high-speed, high-volume process. Assembly line methods further enhanced production capabilities by integrating interchangeable parts and purpose-built machinery, setting the stage for future automation advancements.
Standardization in Manufacturing
Standardization in manufacturing marked a turning point that enabled mass production to become a reality. Eli Whitney’s pioneering use of interchangeable parts in the late 18th century allowed components to be replaced without custom fitting, making repairs and assembly easier. Although initial efforts faced challenges, Whitney’s detailed process documentation laid the groundwork for consistent manufacturing. Standardization focused initially on producing functional, lower-cost products. Principles like division of labor, specialization, and uniform parts supported large-scale manufacturing. These methods reduced waste, lowered costs, and increased efficiency, enabling economies of scale. Standardized processes also improved quality control, ensuring products met consistent specifications. While a precursor to assembly line efficiency, standardization’s role was *paramount* in shifting from craft to industrial mass production, laying the foundation for automation’s future innovations.
The Robotics Revolution and Its Impact on Manufacturing
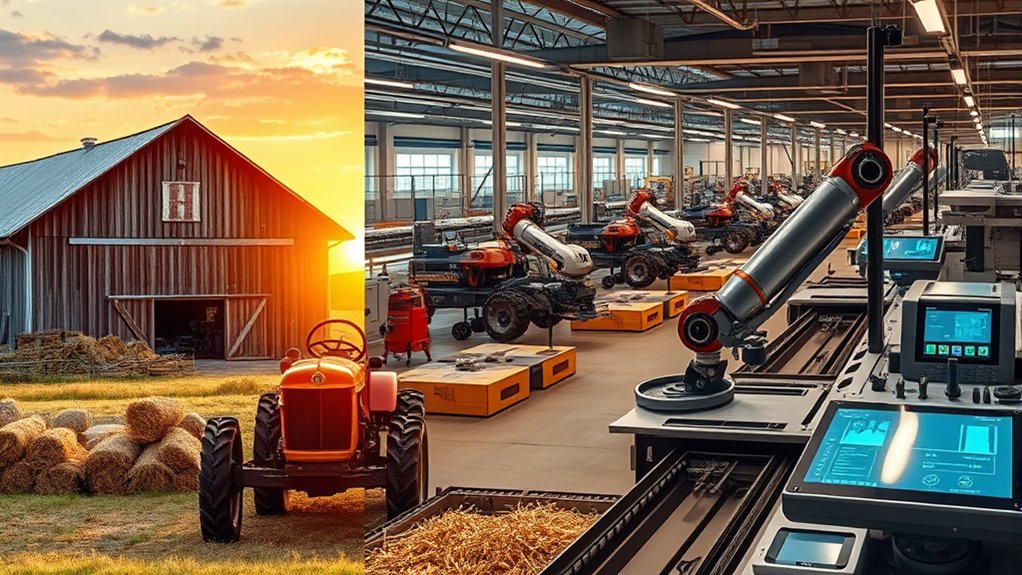
The robotics revolution has transformed manufacturing by considerably boosting efficiency, safety, and precision across industries. You now see robots lifting heavy loads, welding with perfect accuracy, and working in hazardous environments—tasks once dangerous or impossible for humans. This shift has led to:
- Higher productivity, like cars assembled at 100 per hour by 1969
- Safer workplaces, reducing injuries by automating risky tasks
- Greater precision, minimizing errors and improving product quality
- The integration of cybersecurity measures to protect automated systems from malicious threats, ensuring continuous operations
- Advanced control systems enable real-time adjustments and enhanced adaptability in manufacturing processes. These systems often incorporate real-time monitoring to detect and correct issues instantly, further improving efficiency.
Robots evolved from early experiments with Meccano sets to sophisticated multiaxis arms and mobile units. They became more versatile through computer control and multiprogrammability, paving the way for automation that’s faster, safer, and more reliable—changing how manufacturing functions today. Honda Tuning has demonstrated how precise tuning and upgrades can optimize vehicle performance, reflecting the broader impact of automation and technology in manufacturing. Additionally, advancements in automated control systems continue to drive innovation, making manufacturing processes more adaptable and efficient.
Computerization and the Dawn of Programmable Automation
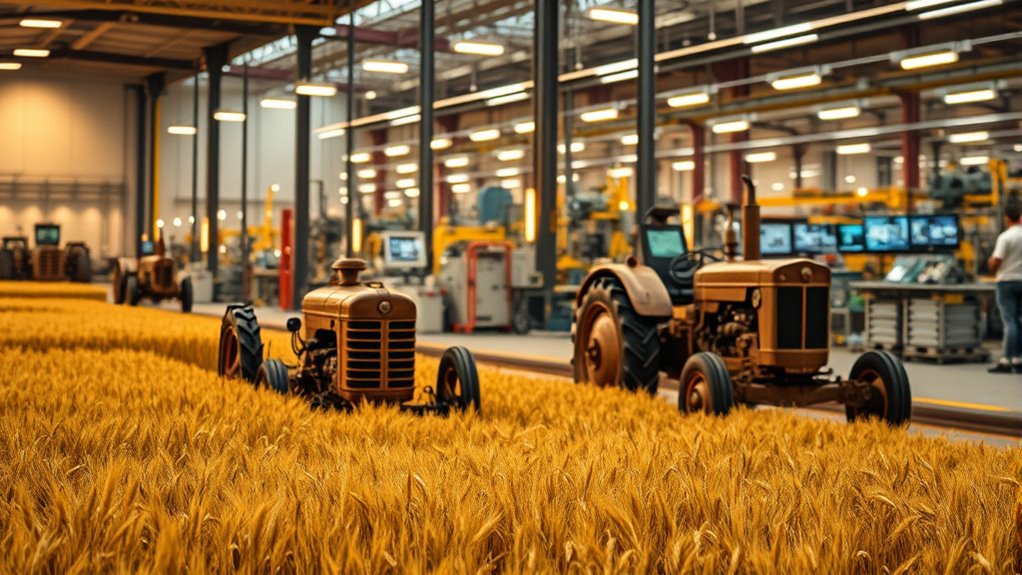
As robotics advanced in manufacturing, the backbone of automation shifted from simple mechanical systems to more sophisticated control methods enabled by computer technology. Early computers provided the processing power and algorithms needed for complex tasks, transforming control systems. In the 1920s, relay logic emerged as a precursor to modern programmable systems, driven by industry’s desire for efficiency and cost reduction. The invention of transistors and integrated circuits made systems smaller and more efficient. By the late 1960s, Programmable Logic Controllers (PLCs) revolutionized automation, replacing hardwired relays with flexible, programmable units. PLCs became industry standards, enabling easier programming, networking, and advanced features. This shift allowed industries to streamline processes, expand production, and require workers to learn new skills, setting the stage for further technological integration.
The Age of AI: Transforming Work in the Era of Intelligent Machines
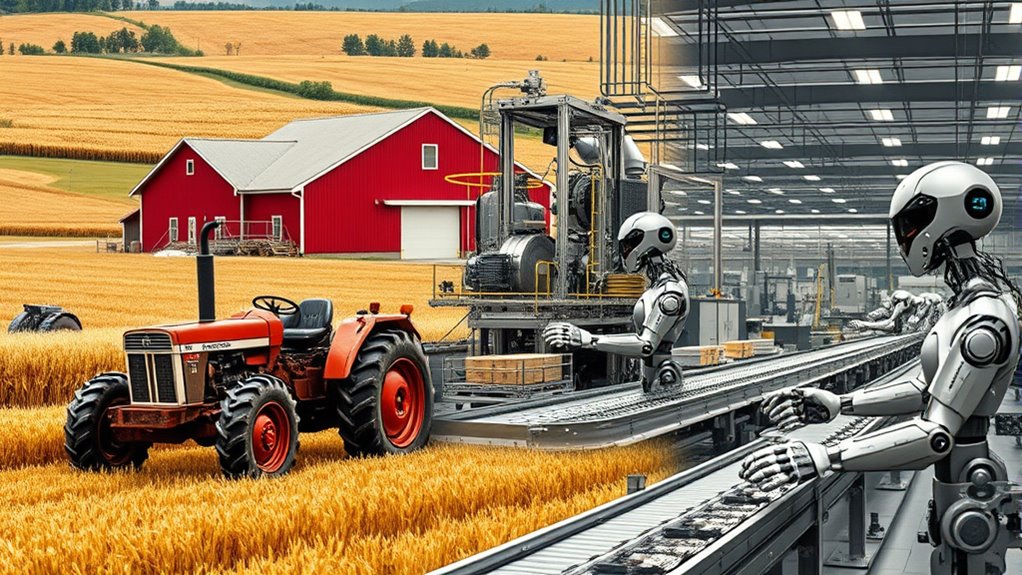
Have you wondered how artificial intelligence is reshaping the workplace today? AI is transforming jobs, creating new opportunities while displacing others. You might notice that:
- Many roles, like medical transcriptionists and customer service reps, are declining due to automation.
- Companies are adopting AI rapidly, with 78% using it in 2024, and reducing workforce where tasks can be automated.
- New jobs are emerging in fields like AI infrastructure, software development, and sectors requiring uniquely human skills like creativity and problem-solving.
- The integration of yoga techniques in workplace wellness programs demonstrates how holistic approaches are valued for employee health and productivity.
- The contrast ratio in automation tools can influence how effectively AI systems interpret complex data and assist in decision-making.
- As automation becomes more prevalent, the importance of employee resilience and adaptability in navigating these changes grows significantly.
- Additionally, fostering dynamic communication skills among employees can help organizations better manage the transition and maintain a cohesive work environment.
- Awareness of cultural self-image and confidence can influence how employees adapt to technological changes and upskill themselves.
While AI displaces some roles, it also boosts productivity and opens avenues for specialized employment. However, it raises concerns about job stability, social mobility, and the value of education. The workplace is fundamentally evolving in this era of intelligent machines.
Frequently Asked Questions
How Did Early Mechanization Influence Labor Practices and Worker Safety?
Early mechanization changed your labor practices by turning skilled crafts into repetitive factory tasks, speeding up work, and enforcing strict hours. It also shifted work from home to dangerous factory environments with little safety, exposing you to hazards. Long hours and unsafe conditions increased fatigue and injuries. While costs dropped and production grew, your work became more regimented, less satisfying, and often riskier, impacting your safety and job satisfaction.
What Were the Economic Impacts of Electrification on Global Industries?
You see, electrification transformed global industries by boosting efficiency, cutting operational costs, and reducing reliance on fossil fuels. It modernized manufacturing, improved transportation, and expanded agricultural productivity. Regions like Asia-Pacific and Europe are leading growth, supported by policies and technological advances. As you look ahead, expect the market to grow notably, driven by renewable energy integration and innovation, ultimately making industries more sustainable and economically impactful worldwide.
How Did Assembly Lines Change Product Customization and Quality Control?
You see, assembly lines transformed product customization by shifting from mass production to flexible, modular systems that let you vary products without losing efficiency. They also improved quality control through specialized tasks, real-time monitoring, and automated defect detection, ensuring consistent quality. Speed increased dramatically, reducing costs and making products more affordable. However, this change also meant workers needed new skills to handle customization options and technical monitoring.
What Ethical Considerations Arose With the Introduction of Industrial Robots?
You should consider that ethical concerns arose with industrial robots because they raised fears about job displacement and worker safety. People worried about losing jobs to automation and the impact on income inequality. Ethical debates also focused on ensuring robots didn’t harm humans, inspired by ideas like Asimov’s Three Laws. Additionally, discussions emerged around responsible design, the need for regulations, and how to balance technological progress with societal well-being.
How Might Ai-Driven Automation Affect Future Employment Sectors Worldwide?
You might see AI-driven automation transforming future employment sectors by displacing some jobs while creating new opportunities. You’ll need to adapt by developing skills like problem-solving and creativity, as these become more valuable. You could work in emerging fields such as healthcare, education, or AI development. Embracing continuous learning will be essential, helping you stay resilient and competitive as industries evolve and new roles emerge worldwide.
Conclusion
As automation continues to evolve, you’re on the brink of a new era where intelligent machines could redefine every aspect of work. Will these advancements lead to unprecedented efficiency or unforeseen challenges? The future remains uncertain, and the next chapter is still being written. One thing’s clear—you can’t ignore how technology is shaping your world. Are you ready to face what’s coming next, or will you be left behind in the changing landscape?